2014年6月21日 (土)
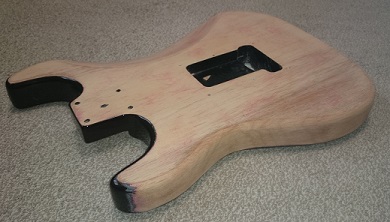
2年以上も完全に放置状態だったLST-Xですが、その理由は言うまでもなく音が最悪だったからです。モッサリしてて、弾いてて不機嫌になるレベルです。
改造完成直後のログには、それなりに良さげな事が記されてますが、今になって振り返ると、自分で手間暇かけて苦労して改造した物を悪く言いたくない負け惜しみ感丸出しで、事実から完全に目を背けていたような気がします。みっともなくて情けないですが。
音が悪い原因は多岐に渡るのですが、最大の要因が、ミリ単位に及ぶ分厚い塗装である事は間違いありません。なので、これを改善するためにはリペイントするしか方法が無いのですが、そもそも厚塗りをしなければならなかった理由が突き板の貼り付け失敗に起因しているため、その突き板そのものから直さなければなりません。これは結構厄介な気がします。
取りあえず塗装を落とす作業を開始したのですが、さすがにラッカーで薄塗りした部分は、硬くて厚いポリ塗装とは比較にならない程にサンディングで簡単に落とせます。画像の状態まで1時間ちょっとで剥がす事ができました。カッタウエイの部分が残ってるのは、単に80番の空研ぎペーパーの手持ちが無くなってしまったためです。
さて、いくらラッカーが簡単に削れるとは言っても、突き板まで手作業で削る根性は無いので、トップ面はどうやって加工してくれましょうかね。
2015年1月3日 (土)
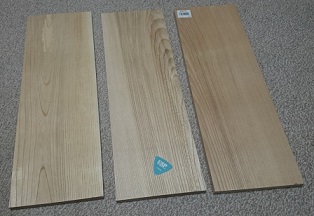
塗装を剥がしかけたまま半年間も放置したLST-Xですが、トップに貼った波打った突き板をどうやって剥がそうかとアレコレ考えた末、最良なのは機械などで一気に削り取ってしまう事なのは言うまでもなく、しかしプレーナーなどの電動器具が使えない環境は百も承知で、強いて言うならホームセンターの工作室の電動トリマーを利用できる程度で、ならば思い切って電動トリマーでトップを10mmくらい削ってしまってはどうかという案に行き付き、削った後に貼るためのトップ材として10mm程度の厚さのアッシュもしくはセンを探していたのですが、これがまた全然どこにも見当たらず、アイチ木材辺りに問い合わせようかとも思っていたところ、いつも工作室を利用させてもらってる近所のホームセンターの工作材料コーナーで偶然にもセン材の12mm厚の板を発見したのです。
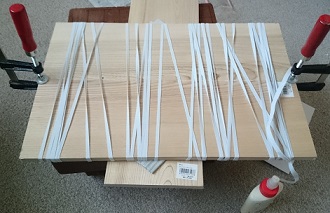
しかし、さすが工作材料のコーナーなので、ギターのボディにはサイズが全然足りず、しかもシーズニングもろくに行っていないようで、数枚あった板のほとんどが反っていたり波打っていたりと、小中学生が工作の材料にするにしても使えないんじゃないかと思える程に酷い物ばかりが置いてありました。それでも他で見かけない、ある意味では貴重なセン材なので、取りあえず程度のいい板を選別して3枚を購入しました(ピックは大きさ比較のため)。これを自力で貼り付けて、いわゆる3ピースのトップ材にしようという魂胆です。
まずは貼り合わせる面の平坦を出したのですが、これが思いもよらず大変で、空研ぎ400番のペーパーで貼り合わせる面を削っては2枚を合わせて隙間が無いかどうかをチェックする作業を、微妙な隙間がなかなか無くならずにイライラしながら何回も繰り返しました。そしてピッタリと合わさった面をタイトボンドで接着するのですが、このような場合はクランプで圧力をかけて固定するのが必須なのですが、40cmを超えるような大きなクランプは1本で2,000円程度もし、少なくとも3本は必要となると、最初からトップ材をアイモクで買った方が良かったくらいの価格になってしまうので、少ない知識の中で思索にふける事を繰り返し、ズボンやパンツなどのウエスト用のゴム紐を利用しました。これを引っ張りながら何重にも巻き付けると、クランプにも匹敵するくらいの圧力となるはずです。たぶん。
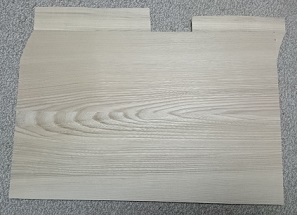
画像に写ってるクランプはズレ防止のための物です。
ボンドが乾燥後、はみ出たボンドも含めて表面を研磨して出来上がったのが下の画像です。LST-Xのボディに合わせた結果、5ピースとなりましたが、木目(杢目?)的にもなかなかいいのではないかと思ってます。
余談ですが、木材を切る時の音や手応えが材によって違うのは当然と言えば当然なのですが、それはギターに加工された際の音を彷彿とさせるのではないだろうかと思ったりしてます。というのも、今回セン材を切った時の感触が音が、軽くて乾いた「カリン!」というものだったからです。ちなみに、ハードメイプルは重くて響かない「ゴリッ!」って感じで、ラワンは軽くてこもった「コリン!」って感じです。
しかし後になって考えてみたら、材を貼り合わせる手間暇かけてまで改造したいって、どんだけ馬鹿野郎なんだろーって思いましたよ。いやマジで。
2015年1月24日 (土)
いよいよLST-Xのボディトップを大胆に削り取る作業を開始します。
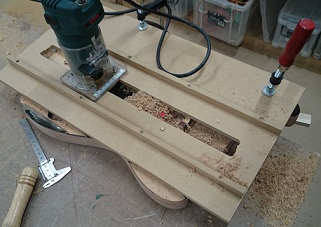
と、その前に、電動トリマーを使うためのガイドを9mm厚のMDFで作りました。ガイドと言っても、ただ単に直線に削れるようにするだけの簡易的な物ですが。
ちなみに、このMDFってやつは屑粉を固めた物なので、切ったり削ったりすると本当に細かい粉になるので、作業をする時にはマスク必須です。
作ったガイドをクランプで固定しながら隅の方から順に削っていきます。いきなり目的の10mmもの深さで削るのは大変だろうと思い、取りあえず今回は約6mmの厚さを削ってみたのですが、これでも結構な力が必要で、相当な力を加えてもトリマーをなかなか進める事ができず、場所によっては摩擦熱で削りカスが燃え出す事もありました。
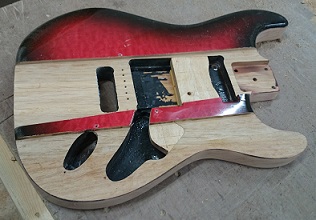
電動トリマーを使用していると削りカスが燃え出すのはよくある事なのですが、今回はラッカーで塗装されている面を削っているため、燃え出すと結構臭いです。
簡易的ではあっても一応はガイドを使用したにも関わらず、ひと通りトップ面を削り終えてみると、理論的には平坦になるハズなのですが、どういう訳か、あちこちデコボコになってます。その段差は大きい部分で約1mmはあるでしょうか。どうにも解せません。
というか、つまりは私に技術が無いだけなんですけどね。
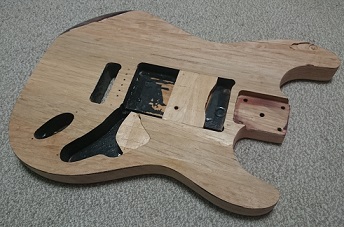
次は約4mmの深さで削っていくのですが、すでに今現在が凸凹なので、当然ながら平坦な仕上がりは期待できません。まぁ、最後はペーパーを使っての手作業による平面出しになるのは想定内なのですが、それでも可能な限りトリマーで平坦に仕上げたいと思います。
しかし、公式サイトでもメールで問い合わせた返信でも「ボディ材はアルダー」という事なのですが、どっからどう見てもアルダーに見えない辺りは、果たしてどう思ったらいいのでしょうか。
まぁ、何だか分からない材だったりする激安ガラクタだからこそ、ここまで思い切った加工ができるんですけどね。これが安物でも一応はちゃんと作られてるスクワイヤーとかフェンジャパ辺りだと少しは躊躇すると思いますし。
2015年2月1日 (日)
先週に引き続き、ボディトップをさらに削り込んでいきます。
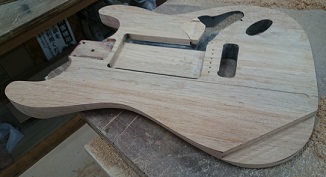
ぶっちゃけ、前回は初めの作業だったので、コツというか具合というか塩梅というか、そんな感じの事が完全に情報不足だったので、結果として削った後が凸凹の段々になってしまったので、今回はその失敗を意識しながら慎重に作業を進めました。
具体的に言うと、電動トリマーを押し付ける力加減とか、右から一方的に削るのではなく、左右交互に削っていくとか、1回ごとに削る深さを確認してビットの深さを調整するなどです。
その結果、2時間もホームセンターの工作室に籠りっきりになりましたが、前回よりかは多少はマシな仕上がりになったと思います。
で、今度の改造ではエルボーコンターを無くす予定なので、そこも削ってます。さらに、PUキャビティを埋めていた木片も削り取ったため、弁当箱が復活しました。
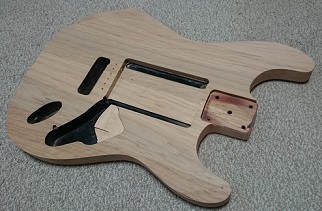
その後は家に持ち帰って、空研ぎペーパーで段差を無くす作業です。
この時、ただ単に凸凹を無くしてスムーズにするだけではなく、真っ直ぐなスケールをいろんな方向に当てながら、可能な限り平坦を出すように研磨しました。でないとトップ板がちゃんと貼れないし、仮に貼れたとしても平面ではなくなってしまうからです。
まだ微妙に1mm程度のなだらかな丘のように盛り上がってる部分もありますが、とにかく北風が強くて劇的に寒かったため、今日の作業はここまでで断念しました。
ネックポケットを見れば、ボディの薄さが分かると思いますが、さらに電動トリマーで削る部分があるので、そのガイドを平日中に作る予定です。
2015年2月14日 (土)
電動トリマーでザグるためのガイドを平日中に作成したので、それを持って近所のホームセンターで作業です。
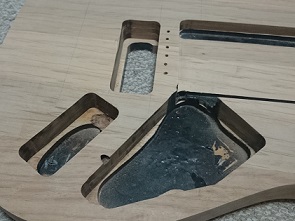
なぜか今日は工作室が混んでいて、おばさんの先客が1人いて、私が作業を始めたら、後から祖母と娘と小学校低学年らしき孫2人が、その後さらにスーツ姿の会社員2名がやってくる繁盛ぶりです。
親子3代は金槌でトンカンと釘を打ったりして、人の良さそうなおばあちゃんは「うるさくてごめんなさいね」などと申し訳なさそうにしてましたが、工作するのにウルサイのは当たり前ですし、私が使い始めた電動トリマーに比べれば可愛いもんです。
どこかと電話してた会社員は、会話できないくらいの耳をつんざくような大騒音に工作室から逃げ出していきましたが、そんなんは知ったこっちゃありません。工作ってのはうるさいもんですから。
で、コントロールキャビティとアウトプットのザグりとシンクロのイナーシャブロックの部分をザグって上の画像のようになりました。このように加工したという事は、お得意の穴埋めをするという訳です。
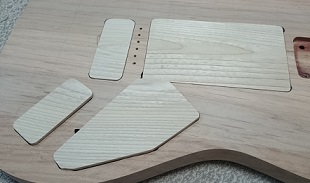
そのための材を同じホームセンターで買ったセン材の板をカットして作ったのですが、このセン材の厚さが約12mmなので、PUキャビティ以外は2枚重ねとなります。
全部で8枚カットした木片を現物合わせで削って形を整えて埋め込みます。下の画像は接着前に仮組みしたところです。
イナーシャブロックの部分を埋めるという事は、当然ボディバックのスプリングキャビティも必要なくなるので、画像には写ってませんが、そちらも埋めるようにセン材をカットしてあります。
以前までは「使用頻度が低いからホームセンターの工作室で借りればいいや」と思っていた電動トリマーですが、最近は「これだけ使うんなら自分で買った方が便利かもしれない」と思い始めてます。もちろん近所への騒音も考えなきゃですけどね。
2015年3月14日 (土)
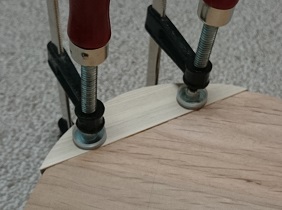
丸々1ヶ月間も更新しなかったのは、インフルエンザで寝込んでいたり、そのために1週間も仕事を休んだ穴埋めで残業やら土曜日に休日出勤したりやらで、ギターをいじってる時間が取れなかったからです。
前にも書きましたが、今回はエルボーコンターを無くすので、その部分もセン材で埋めます。20mm近くもザグったので、厚さ約12mmのセン材2枚(1枚は予め電動トリマーで削って薄くしてあります)を貼り合わせて埋めてます。
一通り全部のザクった穴に形成したセン材を埋め込み、タイトボンドが十分に乾燥したのを確認してから、出っ張った部分を空研ぎ80番のペーパーで削って平面を出したのですが、このセン材が思いの外と言うか、予想以上に、本当にビックリするほど論外に思いっ切り硬く、削っても削っても一向に形が変わらないので、マジで途方に暮れました。
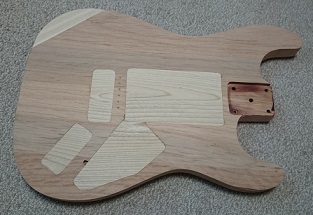
ほんのわずか2mm程度の出っ張りを無くすために、ペーパーを何回も取り替えつつ約30分もの時間をかけて奮闘し、その間にも右腕は何度も麻痺して脱力するので、その都度マッサージを施して回復させながら、ようやく何とか1ヶ所だけ平面が出せるといった感じの作業です。
きっと電動サンダーがあれば苦労しないんだろうなーと思いつつ、でも可能な限り金をかけないコンセプトなので自分が頑張らないとなりません。
ってか、ホームセンターの工作室の電動トリマーで1mmでも削っておけば多少でも楽をできたんですけど、それに気付いたのが作業が終わってからだったので思いっ切り後悔しましたよ。
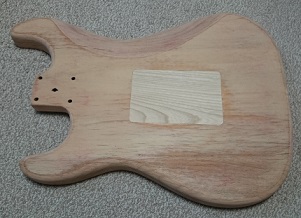
本当にマジで大変な苦労をした甲斐もあって、どうにかこうにかトップとバックで平面を出す事ができました。もちろんコンター部分もちゃんと整形しました。が、右腕は完全に死にました。多分、明日明後日辺りには強烈な筋肉痛に襲われる事でしょう。
あとはザグッたボディの穴と、それを埋めたセン材との間にできた隙間を、セン材を削った屑粉をタイトボンドで練ったパテで埋めるなど、細かい部分の仕上げをする必要がありますが、それくらいなら残業を終えて帰宅した後でも少しづつ進められるでしょう。
元々はストラトタイプのまま仕上げようと思っていたのですが、あるサイトであるギターを見てから、ちょっと形を変えてみようかなーと画策しています。もちろんまだ未定ですが。
2015年3月29日 (日)
と言う訳で、LST-Xのストラトタイプの形を変えていきます。
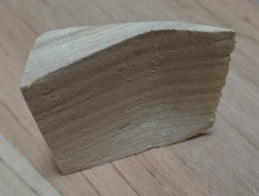
まず最初に考えたのが、ホーン部分の「返し」です。どうも私はそれをカッコいいと思う傾向があって、なのでHONDO Formula 1も一目惚れして速攻で落札した訳ですが、これは多分、中学生の時に見た(当時)イバニーズのPS10の影響が大きいんだと思います。
で、画像のようなパーツをセン材から削り出して作ってみました。いくらPS10の影響ではあっても、さすがにあそこまでの鋭い返しにするつもりはないので、各辺が1対2対ルート3の直角三角形の定規のような形です。
画像でも分かる通りに、いかんせん3Dの曲線なので一筋縄ではいきません。子供が学校の工作の授業で使う彫刻刀を持ち出してきて、チマチマと削っては現物合わせをしつつ、ペーパーで研いては現物合わせをしながら、また彫刻刀で削るを繰り返しました。
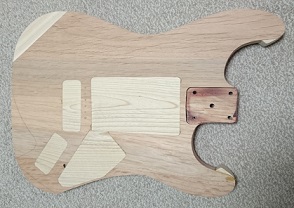
手間暇かけた甲斐あって、それなりに綺麗な形になったと思います。その返しのパーツを貼り付けたのが下の画像です。
良し悪しの批判はセンスやら好みの問題なので置いとくとして、一応は頭の中で想像していた形に近い物が出来上がって満足しています。ボディと返し部分の色が全然違うのは、上からトップ材を貼れば、少なくとも正面から見た場合には目立たなくなるの気にしてません。塗装もするしね。
オーソドックスで保守的なストラトタイプのホーンに、ちょっと攻撃的なイメージがある返しを付けただけだとアンバランス過ぎるので、もちろんこれだけで終わらせるつもりはありません。その証拠に、とは言っても画像では分かりづらいのですが、すでにボディの下の部分の形状が微妙に変わってるのが分かるでしょうか。
次回はさらに大きく形を変えた姿を紹介できると思います。
2015年4月4日 (土)
引き続き、LST-Xのストラトタイプの形を変えています。
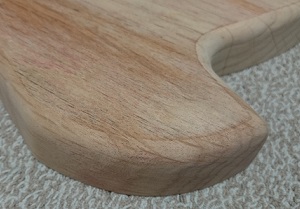
いかんせん、過去にギターの改造を含めて、大掛かりな木工を趣味とした事が無く、なので我が家にはドリル以外の木工用の電動工具は存在しません。なのでボディをカットするのも糸鋸での手作業となるのですが、これの何が難しいって、曲線をカットしながら垂直の断面を保持する事です。
案の定というか予想通りというか想定内というか、やはり断面がデコボコで大きくななめになってしまったので、垂直の断面と綺麗な曲線を出すために、相変わらずこれも手作業による研磨作業で仕上げていきます。
きっとまた明日か明後日には腕が筋肉痛になると思われます。
ちなみに、ボディバックのテーパーというか、角の丸めも完全に手作業で、その部分だけは自画自賛していいと思えるくらいに綺麗にできたと思ってます。
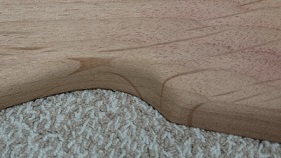
まだ一部の仕上げ処理が終わってないのでボディ全体の画像を載せないため、どこをどうカットしたのか分からないと思いますが、それにしても断面を改めてよく見ると、本当に訳の分からない木目をしているボディ材で、しかも4ピースくらいを継ぎ接ぎしてから表面に薄い突き板を貼って誤魔化すという手の込みようです。
そこまで手間暇かけても激安を維持できるのですから、本当に単なる端材でしかない事実は容易に理解できます。本当にいったい何の材なのかサッパリ分かりませんが、端材であっても音的にはアルダーっぽいから摩訶不思議です。
次回にはボディ全体の画像を載せられると思いますが、デザインセンスの無さは嫌と言うほど自覚しているので、そこは絶対に突っ込まないように、今から注意喚起しておきます。
2015年4月12日 (日)
切った貼ったした結果、このような形になりました。
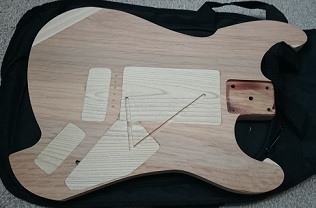
しつこいくらいに何回も書いてますが、本当にビックリするほど論外にデザインセンスが皆無なのと、元がストラトタイプという制限があったため、結局はどこかで見た事のあるような形状を継ぎ接ぎした、何のひねりも工夫もない形になってます。
すでにPUのリード線を通す穴の加工も済ませてありますが、言うまでも無く、PS10とかモッキンバードとかの影響が大きいのは一目瞭然ですね。
まぁ、ひねりも工夫も無いってのは、角度を変えれば無難とも言えなくもない訳で、奇抜すぎてドン引きしたり、すぐに飽きてしまうよりかはいいのではなかろうか、などと自分に言い聞かせてる私です。
で、トップ材を貼るために平坦を出さなければならず、そのような設備を持ってない私は考えた末に、本棚の棚を増設するために使ったパイン集成材の残り板に、子供が学校の工作で使った木片ブロックをネジ止めして、下面に空研ぎペーパーを貼った画像のような物を作ってみました。
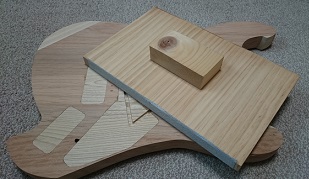
これでトップ材を貼る面を研磨すれば綺麗な平面が出せるだろうと、トップ面全体に鉛筆でマーキングして、それが全部削られて落ちるようにサンディングしてみました。
結果は、確かに以前よりは格段に綺麗な平面が出ましたが、それでもトップ材を合わせてみると、まだ微妙に、それこそコピー用紙1〜2枚程度の隙間ができてる部分があります。なので何回かサンディングを繰り返してみましたが、どうしても微妙な隙間は無くなりません。
あまり削り過ぎてボディ厚が薄くなるのも嫌ですし、どうしたら本当に平面になってくれるのか、また何か別の策を考えるのも面倒臭いので、もうこのままトップ材を貼っちゃおうかとも思ってる私です。
2015年4月19日 (日)
最近はずっと天気が悪くて、しかも昨日は休日出勤だったので、この週末もあまり作業が進められませんでした。
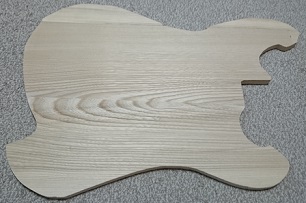
で、行った作業は、トップ板をボディの形状に合わせて大雑把にカットした事くらいです。
上の画像がカット後の状態ですが、こうやって見ると5Pにも関わらず、なかなかいい木目が出てる気がします。というのは自分の作業を肯定したいための単なる思い込みなのかもしれませんが。
実家に電動ジグソーがあった気がするのですが、取りに行くのが面倒くさかったので、たしかホームセンターで120円くらいで買ってきた糸鋸で相変わらずの完全手作業でゴリゴリと切り出してます。むしろそっちの方が面倒くさいだろって突っ込みは無しの方向で。
何だかんだ言ってトップ板は結構大きいので、カットする場所によって歯を右や左に向けて工夫して作業しました。この糸鋸の歯が回る仕組みを考えた人は天才だなって思います。
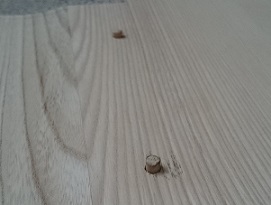
次の工程では大きな圧力をかけてトップ板をボディに接着するのですが、圧力をかけた時に両者がズレないようにダボを打ちこんでみました。
これが予想外に難しい作業で、つまり両者の同じ位置に穴を開けなければならないのですが、当たり前ですが、両者を密着させた状態では外部からマーキングができません。そこで考えたのは、ボディのダボを打つ位置に水性ステインを垂らして、それが乾かないうちにトップ板を乗せてステインを転写するという方法です。
これが取りあえず上手くいって、ピッタリと合わさる位置にダボを埋め込む事ができました。画像に微妙に見える黒いのがステインが付いた痕跡です。もちろん、このダボはPUキャビティをザグれば無くなるようになってます。
さて、今度はどうやって長時間大きな圧力をかけようかと思案中です。この作業のためだけに大量のクランプを買い込むのも馬鹿らしいですから。というのと似たような事をここにも書いてましたね。
2015年5月2日 (土)
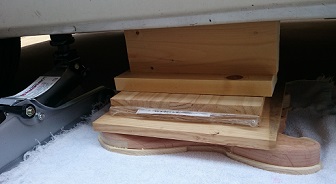
一番上の画像は先週末の作業時のですが、これは車のサイドシルの下部です。つまり、車をジャッキアップして貼り合わせるボディ材にタイトボンドを塗布して仕込み、ジャッキを下ろして車の重量で圧力をかけているところです。
私の車はGD1なので、総重量が1トン程度と軽めなのですが、それでも数百kgの圧力はかかってると思われます。このまま本当は24時間くらい放置したいとこなのですが、やはり野外なので夕方までが限界だろうと思い、約6時間の放置で回収しました。
先週の作業はこれだけだったので更新しなかったという訳です。
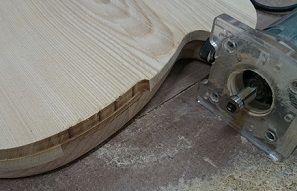
これだけの圧力をかけたにも関わらず、やはり完全な平面ではなかったため、周囲には本当に微妙に隙間が空いている部分が散見されたので、そこにはタイトボンドを流し込んで処置しました。
もう本当に単なる素人の工作レベルの酷い作りですが、丁寧さで言うならギブソンやフェンダーもあまり変わらないかもしれませんね。
いやマジで。
2枚目の画像から今日の作業となりますが、トップ材をボディの形状に合わせるためにコロ付きビットを使用して電動トリマーではみ出た部分を削っています。
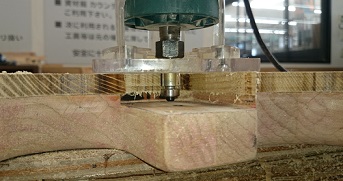
実はコロ付きビットを使うのは初めてなので、かなり緊張しつつ慎重にゆっくりと作業を行ったため、ビットの回転による摩擦熱でトップ材のいたる部分が焦げてしまいました。まぁ、サンディングすれば大丈夫だろうと気楽に考えていたのですが、これが後で困る事になるとは思いませんでした。
計算外だったのがネックポケット部分です。3枚目の画像の通り、ビットのコロが予想外に高くてトップ材の下に入らないため、ここだけ電動トリマーで削れなかったのです。仕方がないので手作業で削ったのですが、狭い場所なので結構大変でした。
この画像では、カッタウエイ部分のトップ材が焦げまくってるのもよく分かりますね。
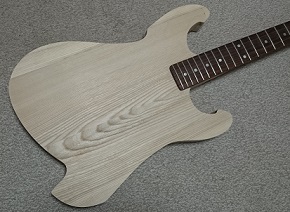
その後、削った部分をサンディングして整えつつ焦げを落とそうとしたのですが、これがマジなかなか落ちなくて大変でした。これ以上削ったらボディの形が変わるだろうって懸念もあるし、かと言って焦げたままではみっともないし。
結局は面倒臭くなったので、焦げは塗装で誤魔化そうと考えて、電動トリマーで削った部分を綺麗に均して終わりにしました。
試しにネックを仮止めしてみたのが4枚目の画像です。
自分では「なかなかいんでないかい??」って思ってますが、果たして一般的にはどうなんでしょうね??
もちろん、すでにブリッジやアッセンブリーをどうするかは決まってますので、今後はそれらに関する加工となります。